

Table of rheology and associated problems AreaĬoating recipes vary by mill, so we don’t have specific information on them. Knowing a fluid's viscosity makes its flow rate predictable under certain circumstances. Viscosity has internal friction of fluids, which causes the fluids to appear thicker when flowing.
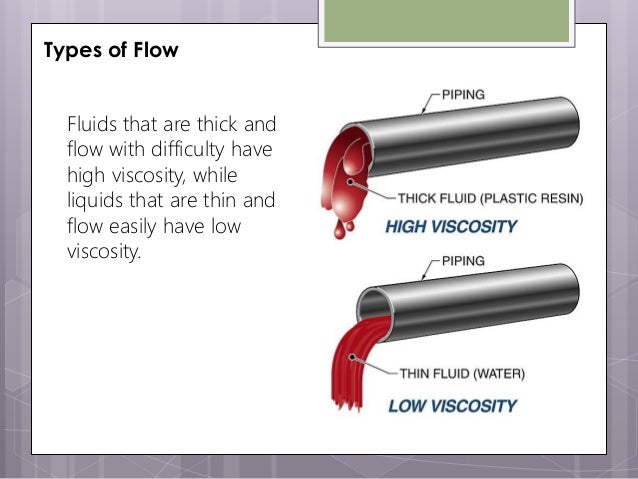
Coating rheogramsįigures 1 & 2 are illustrations showing how different types of coating recipes are affected by shear rate and the problems that can arise when viscosities get out of control.įigure 2 General guidelines for interpreting graphs (see area descriptions below) Viscosity is the resistance to flow, so higher viscosity fluids flow more slowly at a given level of force pushing them along. High high-shear viscosities can cause poor coat weight control, bleeding at the blade tip, and excessive blade loading, which can lead to poor runnability on the coater. It is a good indication of how the coating will respond to high shear rates under the blade tip. High-shear viscosity is not usually done on the coater, but performed in the lab when testing different coating recipes or investigating coater runnability problems. Brookfield viscosity is a good indication of coating solids, problems with the starch cooker operation, blade load pressure, coat weight control, and drying demand. At lower temperatures, the hydrogen atoms in the oleic acid. It is a simple test but very useful for determining operation of the coater. The oleic acid molecules that are in olive oil are made up of carbon, hydrogen, and oxygen atoms.

Low-shear viscosity is the most often performed test in the control of the coating process. Specifically, in coating rheology, it is the measure of the resistance of a coating formulation to an imposed flow. Viscosity is the resistance of a material to flow. Coating rheology is measured with low shear (Brookfield) and high shear (Hercules) viscosity instruments.
